Moving Air
Empty movements are among the most significant operational and commercial constraints in transportation, affecting both passengers and freight flows alike.
About 20% of all containers are moved empty as they are being repositioned.
Empty miles
seem to be the transportation industry’s oldest enemy, it causes profit loss and refers to instances where trucks are on the road without any cargo, usually due to lack of nearby loads headed in the same direction as the driver.
This gets harder for FMCGs since the transport of goods is governed by other factors such as chosen packaging, means of transport and the actual good storage.
They also represent a major waste of fuel, time, labor and contribute to traffic congestion and carbon emissions.
Even when there is advanced cubing software, this software focuses only on the planning side of the problem, while in reality direct route delivery trucks end up wasting space, or as we say it transporting air.
Top 3 Strategies
Improve Shipment Density/Load Utilization
Reducing Logistics Costs
Ensure Perfect Order Fulfillment
Cost per Stop
The productivity of a delivery process is measured by the time used and by the quantity of goods delivered on as single delivery. The time factor means that delivery productivity is restricted by the available time per day (and is dependent on the driver’s maximum shift time). Since each stop consumes a certain amount of time the typical daily number of stops (in the logistics service provider industry it is called “stop factor”) is betwween 15 and 20 per day in LTL.
The weight factor implies that in case of large shipments the stop factor will be lower than 15-20, because the vehicle load capacity will be reached already with few deliveries. This load capacity (approx. 2.8-3.2 t for a truck with 7.5 t overall weight) allows for about 15 stops of 0.2 t each.
Time restriction is the most relevant one in typical LTL (and DSD) operations since for delivery routes with lower stop numbers, the costs per stop increase correspondingly.
On the level of the individual delivery it is still necessary to distinguish between the delivery stop on the one hand and the delivery of one order on the other hand. In case of one order being delivered in one stop both are identical. If, however, two or more orders are delivered withing the same stop, the stop costs are allocated so several orders and the delivery costs for each individual order decrease to 1/2, 1/3, 1/4, etc. of the stop costs.
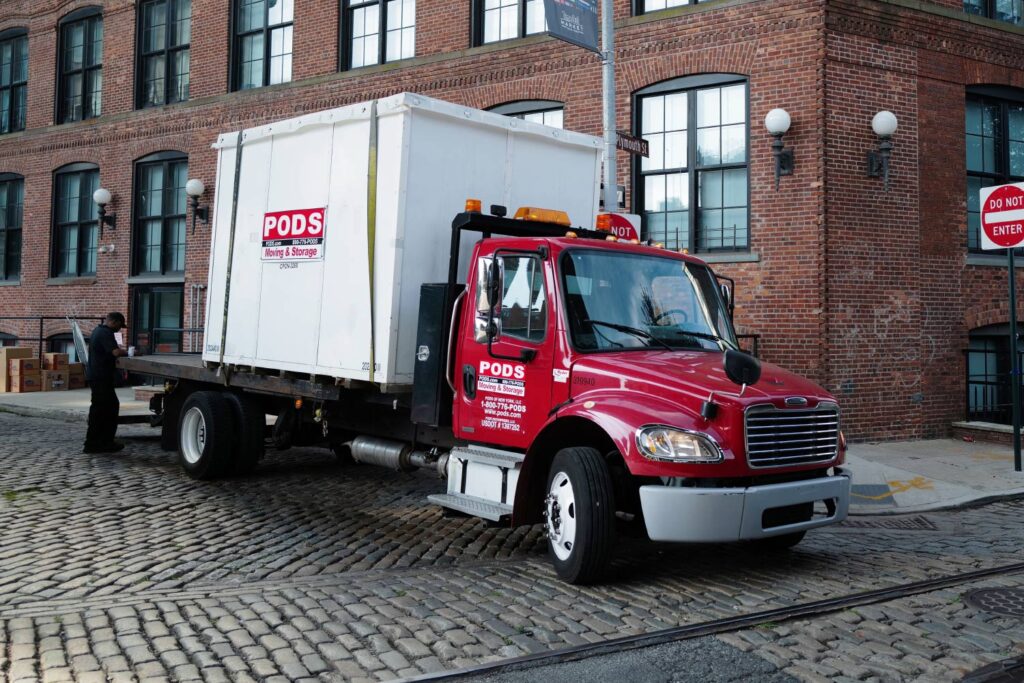
Since time is the most relevant restriction to target and optimize then the following activities are critical:
QA walk-around for Orders
Automatize and optimize the time your DSD trucks spend on the depot gates so that this process can be as fast as possible.
Idle Order Fulfillment Time
Identify idle times in order fulfillment and time on ramp.
Ramp Congestion
Optimize DSD time by eliminating Ramp Congestion by timing individual vehicle to ramp and individual order.
Evaluate DSD Suggested Models
Measure times, individual orders and costs regularly in order to detect errors in the DSD delivery planner.
How can Braingine help?
Direct Store Delivery is an expensive mode of distribution, so the focus of managers is to shift on how to perform DSD operations efficiently.
Braingine performs automatic, real-time measurement of time and motion that help you find bottlenecks you can then fix. Because as Peter Drucker said “if you can’t measure it, you can’t manage it.“
Braingine delivers real time analytics so you can measure
- QA walk-around for Orders
- Idle Order Fulfillment Time
- Ramp Congestion
- Time and Motion
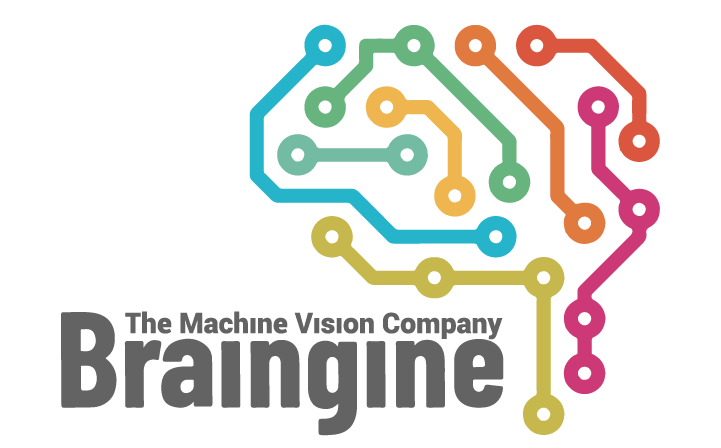
Schedule a Call Today!
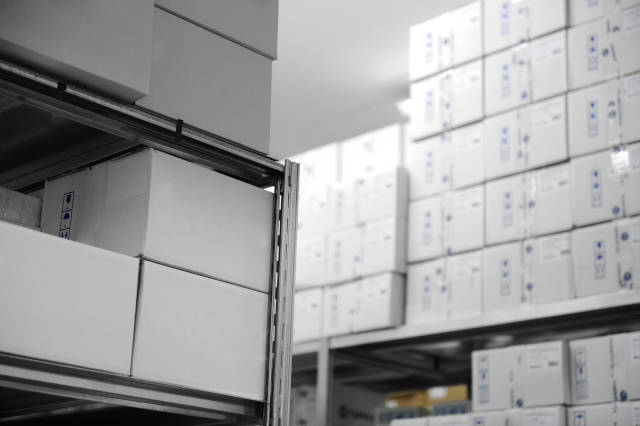